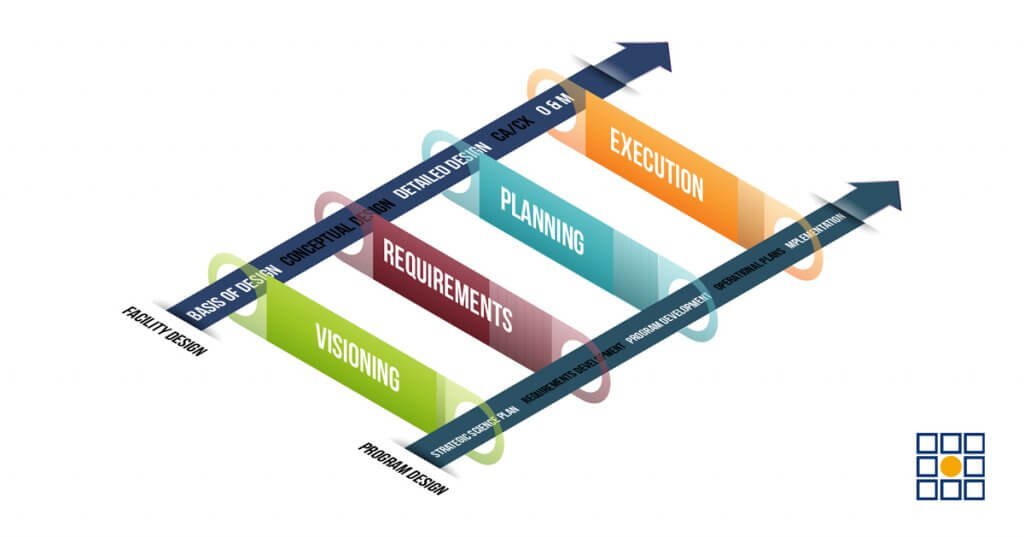
Operational Planning for Biosafety and Biocontainment Programs
10.10.19
By Ryan N. Burnette, Ph.D., Director of Biosafety and Biosecurity Programs
National Biosafety Month is always a good reminder that practitioners of biosafety have made great progress over the past year advancing the field, raising awareness, mentoring new biosafety professionals, and sharing successes in respective programs.
In appreciate for National Biosafety Month, this will be the first of four blog entries from different staff here at Merrick & Company contributing their thoughts and expertise to different aspects of biosafety and biosecurity.
I wanted to start this blog series for the month of October by sharing some information on the benefits of operational planning for biocontainment laboratories, as we have learned through current efforts being led by Merrick. Let’s start by comparing the central dogma of biocontainment laboratory design and construction projects. Typically, a biocontainment lab project begins with the development of a Program of Requirements (POR) that captures the who, what, when, where, and how that will influence the design of the lab. This is often captured in a more detailed manner in conjunction with a Basis of Design (BOD). The design process begins with conceptual-level documents, usually providing the lab layouts and other significant details. Detailed design is exactly what it says: details! This is where the design is completed to a level that contractors can construct the lab. From here, the lab is built (if only it were that simple…) and commissioned. In an extremely simplistic approach, the central dogma of biocontainment lab development looks like this:
Plan > Design > Construct > Operate
I wonder how many readers of this blog have been a part of a biocontainment lab design and construction effort as an end-user to find that some of the requirements identified early in the process evolved or matured by the time you took occupancy of the fully-commissioned lab. Or, you found that new models of significant research or diagnostic equipment became available, only to find they had new requirements that weren’t planned for. Or perhaps new programs would dictate different functions for different areas of the labs. The possible permutations are vast.
Merrick has led efforts with major biocontainment programs to support Operational and Transitional Planning that occurs alongside the design and construction processes to help address many of those issues and others. The basic formula is 1) Identify a model by which the idealized, steady-state facility and program will operate, 2) identify, organize, and prioritize all relevant requirements in support of that model, 3) development of an integrated schedule to guide the harmonization of facility completion, occupancy, and start-up, and 4) development of discrete program plans that will support operational program areas. The figure below provides an overview of a coordinated operational planning process in alignment with design and construction.
The Operational Model:
Operational Models provide a foundation to align stakeholders on how the facilities and programs will operate in an idealized manner, much like a facility-specific performance standard. Operational Models should clearly define new (or recapitulate existing) vision and mission statements, define the stakeholders and partners, explain the roles of leadership, provide an updated version of the biocontainment facility capabilities and services, define a robust culture of responsibility and accountability, identify and describe the various operational programs (e.g., biorisk management, information technology, security, etc.), and provide a foundational overview of management systems relative to training, procedures, and emergency management. Imagine the benefits of being a biosafety officer with the opportunity to define your biorisk management program expectations around the facility, rather than have the facility, equipment, etc. forced upon you. The end result of this process is a defined guidance and expectations document from which all operations and planning thereof will be derived.
Requirements Gathering:
Let’s face it: we may have missed a few requirements back in the design phase that we’ve discovered are going to be pretty important. This phase is vital to collect not only requirements that were missed during the POR or BOD, but collect requirements that are new and/or changed, as well as do a more thorough job of capturing requirements across functional programs. For example, it is a requirement that the lab must have a critical piece of equipment. And it is critical that the room the piece of equipment will be housed in must have a high-speed data drop. But have we accounted for the fact that this piece of laboratory equipment must have access to that data drop? Have we captured the fact that this new model of lab equipment generates twice the data the version identified during the design phase? As another example, let’s say a particular room was intended to house instrumentation and programs for molecular diagnostics. But another building on campus will have better capacity and this space is no longer needed. Instead, it would make more sense to use this space for another purpose. Will the “old” design still provide all the requirements for the “new” purpose? This phase captures all of those requirements and brings them together into cohesion. Additionally, the requirements process, built from the Operational Model, will also identify requirements related to occupancy and start-up, all the way down to the who, what, where, when, and how.
Integrated Scheduling:
Operational planning of biocontainment labs requires mastery of aligning all of the details that were collected from the requirements gathering phase. What needs to move first? Can you shut down operation of a program before you stand it up in the new facility, or do you need to have the new program stood up in duplicate temporarily? What equipment needs to be in place for commissioning, versus what can wait for later? What dozens of items and program areas need to be functional before research or diagnostics can start? Do you know in which order, or in tandem, that they need to be instituted? Development of an integrated schedule provides the answers to these questions and yields a clear path forward that becomes the recipe for the entire transition process. Additionally, the integrated schedule makes note of significant construction and commissioning milestones- this way, no operational or transitional planning gets ahead (or behind!) of the facility completion process. This is one of the significant benefits of operational planning that decreases the time from facility handover to operation.
Operational Plans:
It’s all come down to this: each program area has their respective plans for instituting their programs. We’re not suggesting that the entire biorisk management program, inclusive of policies, procedures, training, manuals, etc., should be complete at this point. Rather, an operational plan provides the person in charge of the biorisk management program, for example, with a plan to bring about the program. These plans become the framework and scaffolding for which all of the programs 1) identified in the Operational Model, 2) which requirements were collected and updated, and 3) were built into a integrated schedule. In a way, it’s sort of like receiving the cheat-sheet to make program functional quicker and with updated requirements.
Summary:
The process described above has the potential to change the age-old paradigm of biocontainment facility and program design. Operational planning reduces the gap that often occurs between facility completion and operations. This has the ability to save institutions significant cost. Further, it gives all stakeholders the ability to align on the same path forward. We encourage you to view a recent webinar on Operational Planning here and hope this information serves you well in your next biocontainment planning endeavor.
Thank you, and happy National Biosafety Month!