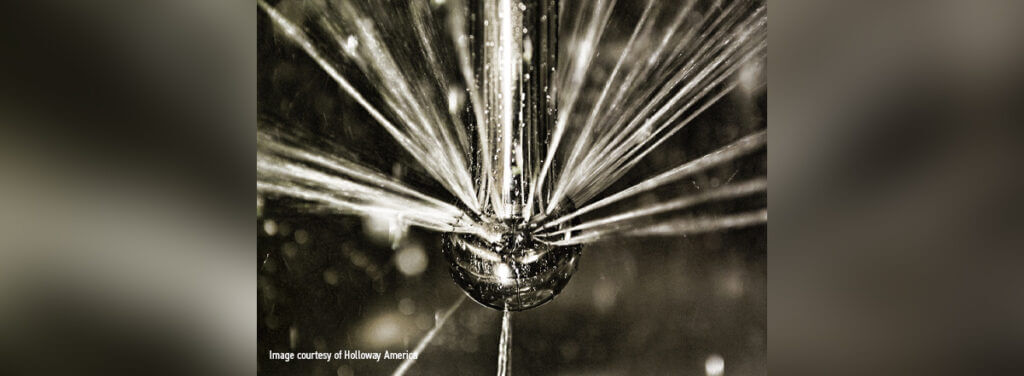
Choosing the Right Spray Devices for Your Fermentation Project—Four Things to Know
10.13.21
By Cole Weinland, Project Engineer, Bioprocessing
Clean-in-place (CIP) spray devices (sometimes called spray balls) are extremely versatile. While this content focuses on industrial fermentation projects, spray devices may be found across many industries, including marine and fuel transport, food processing, biomatter-conversion facilities, and pharmaceuticals. This market-driven versatility has resulted in a wide variety of spray devices from dozens of different suppliers.
The first question to ask when choosing the right spray device for your project is, “How clean does the equipment have to be?” The answer generally depends on the process and end user requirements. The purchaser must convey those requirements to the supplier. Below is a breakdown of four important topics to discuss with your spray device supplier when choosing the right device for your project.
1. Pay Close Attention to Geometry
- Complexity – Most spray devices use a liquid cleaning agent, so consider how easily liquid will flow on the surfaces of the equipment. In fermentation projects, this usually refers to vessels, tanks, and piping. Sharp edges and crevices may prevent the free flow of the cleaning agent. “Smooth and simple” geometry is preferred. All appurtenances inside the equipment must also be cleaned. Keep in mind all internals create shadow zones where the spray cannot reach (like mixers, baffles, and vortex breakers). Complete coverage on internals may require multiple devices.
- Drainability – In most cases, the cleaning agent must be completely removed to avoid process contamination after the cleaning cycle. This is a critical design factor, so make sure there can be no pooling anywhere and that the drains follow hygienic design standards (i.e. flush, sloped, etc.).
2. Choosing the Appropriate Type of Spray Device
- Static – The static spray device is permanently installed and stationary. It sprays the equipment with cleaning agent in many directions. The basic design is a spray head with drilled holes that function as spray nozzles. The advantages of static spray devices include quicker CIP cycle times and no rotating parts. Static spray devices are usually better suited for smaller-sized applications.
- Rotating Head – This class of permanently installed spray device spins 360° and can be hydraulically driven by the cleaning agent. Alternatively, a mechanical external driver may be used. Holes or slits are used as spray nozzles. This type of spray device is efficient for cleaning large surface areas but may require longer CIP cycle time.
- Retractable – A retractable spray device is telescopic and uses static or rotating heads. This type is used when a permanently installed device is not suitable for the process or equipment design. This may be necessary for large ducting or complex reactors.
- Programmable – A programmable spray device is customizable for specific spray patterns. While more expensive to design and build, programmable spray devices are more suited for complicated geometries and offer unique spray coverage.
Each type of spray device varies in price. The least expensive device to purchase is static and the costs increase from there. However, considering operational costs, using a static device may result in an increased cost over time compared to other types. Work with your supplier to determine the most cost-effective type and/or combination for your project type.
3. The Importance of Process Substrate Characteristics
Chemical properties of the substrate to be cleaned, such as viscosity, caking tendency, staining tendency, abrasiveness, and sludge-ness, must be disclosed to the spray device manufacturer. These properties influence the “blast force” and time required to remove the substrate from the equipment surface area.
The substrate characteristics impact the upstream system design of the spray device(s). The supply pressure and flowrate of the cleaning agent determine the blast force of the spray device. These requirements fall on the system designer and must meet the spray device manufacturer’s recommendation to ensure the client’s cleaning standards are met.
4. Validation is Critical
How can you ensure adequate cleaning and avoid a shutdown? Validation requirements vary by industry, but below are some industry best practices for validating coverage in existing configurations or conceptual design:
- Riboflavin testing – During riboflavin testing, a riboflavin solution is sprayed across the inside of the equipment, the equipment is sealed, and a cleaning cycle initiates. Spray devices are fed with water to wash the riboflavin from the equipment and internals. After the cycle, the equipment is opened and inspected with ultraviolet light. Since riboflavin reacts to UV light and glows, any shadow spots are easily identified.
- Simulation / Shadow Study – Using computational fluid dynamics or vector analysis, spray coverage can be modeled by computer. A computer study is useful for large equipment that would not be easily tested using other methods. Results from this can be used to change the design before fabrication.
- Visual – A simple visual internal sight inspection can be conducted after a cleaning cycle. If anything is seen coating the walls, the inspection has failed, and the user will need additional spray devices or design modifications.
- FAT “Factory Acceptance Test” – If practical, require the spray device vendor to test their devices on the end user’s equipment in their own factory. The end user will need to agree to which tests are to be performed. Post-test results can result in beneficial recommendations.
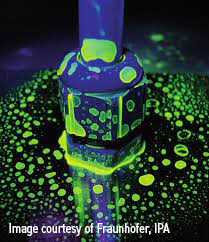
Riboflavin Test
Spray devices combined with other hygienic practices are a proven cost-effective way to protect your process from contamination. However, there are multiple factors to consider when choosing what type of spray device is right for your project. Make sure to speak with your supplier and communicate with the end user to determine which device is the right fit.