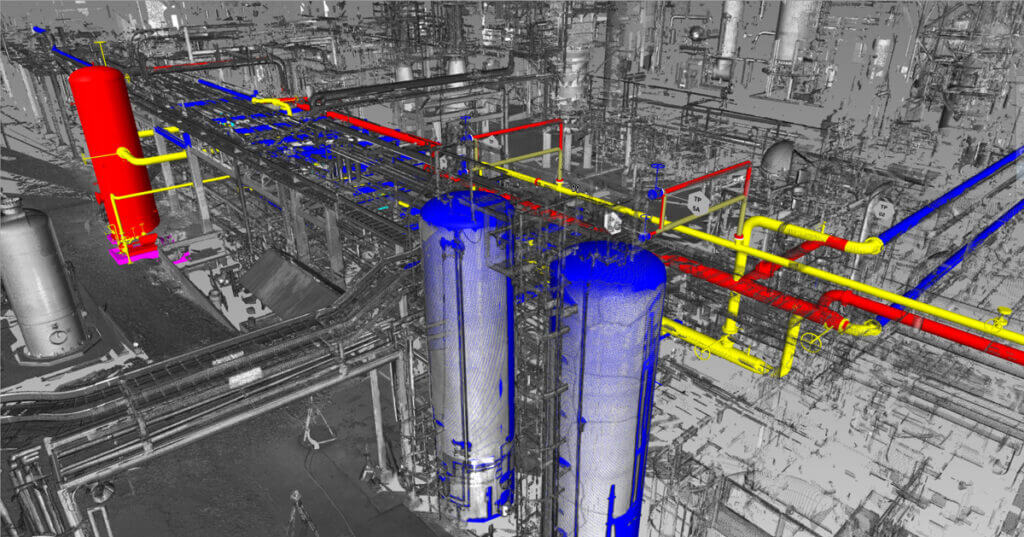
LiDAR: A Safe, Efficient Way to Collect Information for Power Clients (During COVID and Beyond)
08.19.20
By Michael Varner | Business Development, Power
Merrick routinely uses light detection and ranging (LiDAR) in both new and retrofit projects for our power clients. The ability to walk into an operating power plant and collect precise layout and dimensional information is invaluable. Gone are the days of designers and engineers crawling through equipment and racks to manually measure. Instead, a point cloud is collected via the LiDAR equipment and distilled back in the office, minimizing the staff that must be on site to collect the data. The point cloud is then used by the staff to “walk through” the site and accurately lay in the new work… all in CAD. Lidar is a safe and efficient way to collect plant data, both during the current COVID-19 pandemic and beyond.
Laser scanning and LiDAR technology has been used as a design tool by engineers, designers, and architects for decades. LiDAR is a remote sensing method that uses light in the form of a pulsed laser to measure distances from the sensor to objects around it. These light beams generate precise, three-dimensional information about the shape of the surfaces being scanned. LiDAR technology allows for the 360-degree capture of existing buildings, piping, support steel, process equipment, and other items within a plant.
The benefits of incorporating LiDAR technology into the project design cycle are both proven and undeniable. LiDAR enables a project team to accurately design, compare, measure, plan, and coordinate with the site from the office and/or remotely. With a typical measurement accuracy within 3 cm, this technology provides superior clash detection and visual representation of the existing (and new) plant infrastructure. LiDAR is also a great tool for developing as-built models when limited or no reference drawings are available.
The software to analyze the LiDAR data and create the 3D point cloud(s) has improved significantly over the years. Nowadays, the point clouds are compatible with commonly used design software like SmartPlant, PDMS, MicroStation, AutoCAD, Revit, and Navisworks. Project teams commonly review 3D models built with LiDAR data. Generally, using LiDAR technology as a design tool improves engineering effectiveness by preventing costly mistakes, reducing rework, and maximizing schedule.
While there is an upfront cost to using LiDAR, the overall cost-saving benefits to the project are well known and documented. The use of LiDAR is a good investment in most cases where equipment and materials must be retrofitted into existing plant infrastructure. Moreover, as more project teams are forced to work remotely, and customer site visits are discouraged because of COVID-19, the benefits of LiDAR technology are particularly beneficial. These COVID-19 restrictions make the use of LiDAR laser scanning overwhelmingly compelling.
Merrick has used LiDAR for our power clients with great success. Here are a few examples:
- We developed a combined heat and power plant at a manufacturing facility. The new equipment had to be shoe-horned into the existing site, with numerous connection points and potential interferences. Point clouds taken from both inside and outside the main building were stitched together to create a 3D model of the entire project area, including building steel, existing foundations, and equipment. “No-fly” zones were created to ensure the new design did not interfere with existing access ways. The result was a highly integrated design with minimal interference and impact to the existing facility.
- Merrick developed improvements to a gas relief piping system in a very congested industrial facility. Existing piping was densely packed into existing racks, with the new work in some cases adding to, and in some cases replacing existing piping. LiDAR scans were critical in obtaining accurate as-is layout information, leading to effective design development. Some elements of the design required precise installation of new work in locations where physical access was difficult, if not impossible, prior to construction. The use of LiDAR allowed precise design of the new work with a relatively low cost of field data collection.
- We used LiDAR to support the conceptual design of a new pollution control system for an industrial manufacturing facility. While the majority of the system was new work, the integration of the new system into the existing flue gas ductwork was critical. The ductwork was sizable, reaching from grade to approximately 50’ above grade, including multiple tie-points. A low-resolution LiDAR scan performed by a one-person crew was able to collect sufficient data during a short site visit to allow designers to develop several ductwork options to support the feasibility study.
LiDAR has become more cost effective and commonplace as a design tool in recent years due to significant advancements in software technology to evaluate and build the point clouds and improvements in scanner technology that allow more accurate data collection and data resolution. LiDAR systems allow scientists, engineers, surveyors, and other professionals to examine both natural and manmade environments with accuracy, precision, and flexibility.